
The final decision rests with the product life cycle team and their objectives. The cost to fabricate and the time needed to produce parts are minimized using 3D printing. 3D printing brings advantages that are difficult to match with traditional manufacturing technologies. CNC machining has been and will continue to be, a viable means of fabricating parts. There's certainly merit in both CNC and additive manufacturing. This may even be more sophisticated as part labels may be printed such that they do not show up at all, and are somewhat indelible, but can be scanned or identified by using say an infrared reader. This is an important benefit of additive manufacturing in lieu of CNC machining or other metal forming processes. With the detailed capabilities of 3D printing, a part may be labeled with a barcode and other specific information by printing it on the part, as part of the fabrication process. Such a process is an adjunct, but usually separate from the part's fabrication. Labeling parts, however, sometimes requires a separate process whereby a label must be printed or affixed to a part. Parts may be barcoded or labeled with key information that allows their inventories to be finely controlled. Maintaining and tracking parts inventory is crucial nowadays. One significant advantage of producing parts with additive manufacturing or 3D printing is the possibility of printing specific part labels on the part, using the 3D printer. What's more, the volume of the tool need not be small in volume. This allows a production tool to be manufactured from additive processes. CNC machining usually requires longer lead time material, generates more waste, and is not nearly as fast as 3D printing.īy using additive manufacturing and the right printer, complex geometries may be achieved at moderate production volume, with much less time and effort.įor example, Stratasys FDM technology can print several high-strength thermoplastics that can withstand the pressure of forming thin-gauge metal. Forms may be printed with a specific amount of material, follow complex patterns, optimally utilize available material, and produce such parts faster with less waste.

It allows multiple iterations of the fabricated part using different designs and complex geometries. When the Design and Specification of the Fabricated Part is ComplexĪs with the custom die or brake tool, parts are often complex and require more sophisticated geometries.Īdditive manufacturing is ideal for complex parts. Additive manufacturing of the tool saves time and cost over traditional machining methods. It can be produced faster with less waste. In addition, FDM is also well suited for offset and flare tooling in thinner gauges of sheet metal. It is a better option for volumes ranging from 100-500 cycles. If a custom tool is needed, the cost and lead time to produce it is more favorable with additive manufacturing.Īdditive manufacturing, using a fused deposition modeling (FDM) 3D printer is quite capable of making the custom metal forming die, vice CNC machining. This disrupts the design process, resulting in added costs. Thus, it requires specific material that may have a long lead time and is not readily available. The need for a custom tool is often discovered during the design process after fit and function testing.
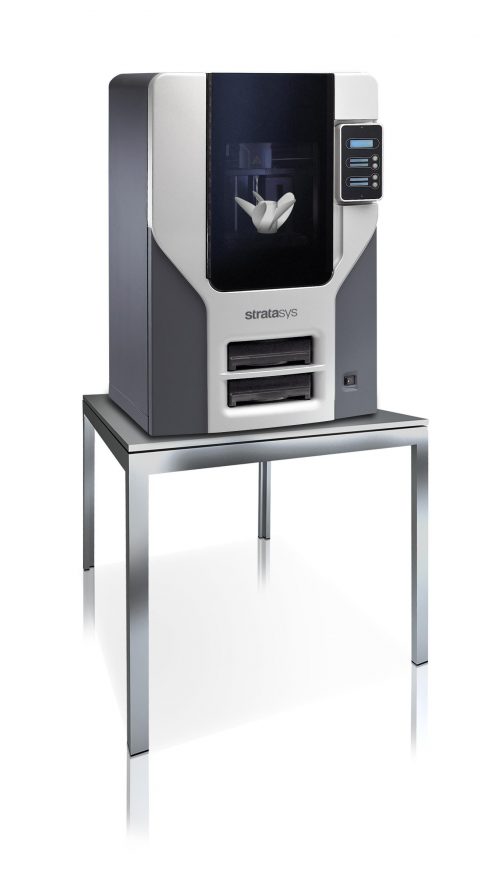
However, this option is not ideal when a custom tool is needed.
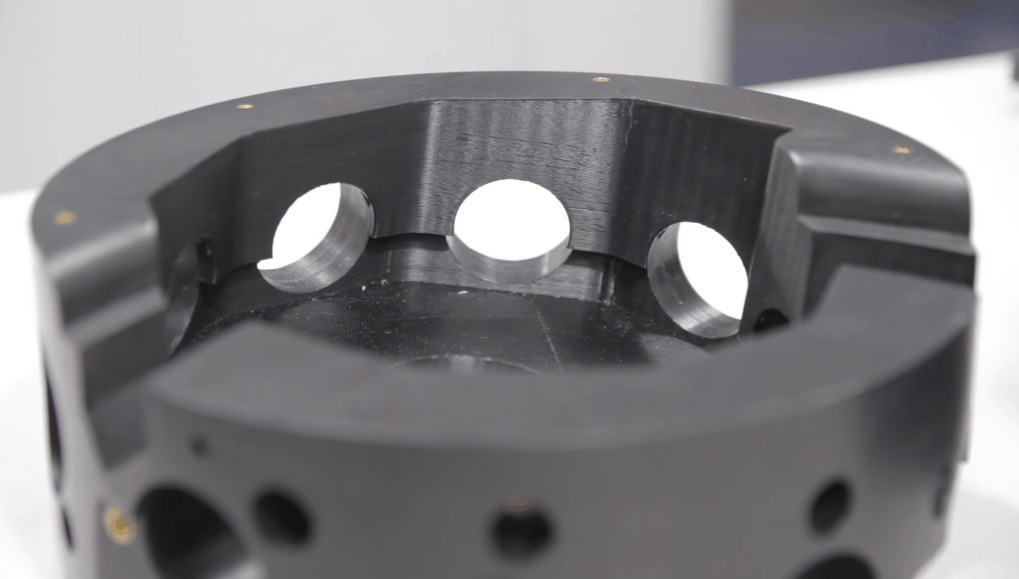
The tooling is available commercially off-the-shelf (COTS) from several manufacturers in standard geometries. Traditional methods create parts that are machined from tool steels such as A2, D2, or 4140. For example, additive manufacturing has been used to create custom metal forming dies and press brake tools instead of traditional methods. When Specifications and Designs Call for Customized Parts and ToolingĪdditive manufacturing expedites the fabrication of customized tools, – creating them faster and cheaper.
